absorption rate of recarburizer in casting
Nowadays, most of the foundry smelting equipment is an intermediate frequency induction electric furnace, and more than 50% of the smelting charge used is scrap steel. Turning scrap steel into cast iron becomes a necessary means to increase carbon. According to statistics, we now use more than 30 million tons of scrap steel for electric furnace casting production each year, and the scrap steel consumed by casting is second only to steel mills.
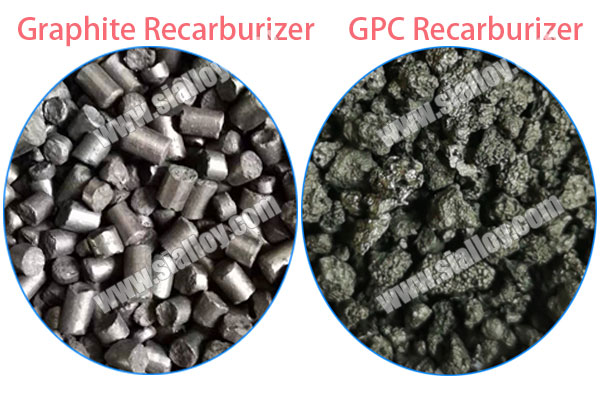
There are two prerequisites for carbon increase in casting:
Firstly,the target composition of the product must be determined first, that is, the chemical composition of the casting product we are going to do.
Secondly,The amount of recarburizer added must be calculated in advance.
To calculate the relative amount of recarburizer added, we need to know three conditions:
1.The ratio of scrap steel to other charge in the smelting charge, and the carbon content of other charge such as recharge and pig iron.
2.The carbon content of the scrap steel used. The carbon content of different scrap steel materials is different, and we can calculate it only if we know the carbon content of the scrap steel.
3.Absorption rate of recarburizer. By observing different foundries and different recarburizers, the absorption rate of recarburizers is roughly 70%-90%.
There are many reasons that really affect the absorption rate of recarburizers. The following analysis focuses on several aspects:
(1)The higher the carbon content in the molten iron, the lower the absorption rate of the recarburizer.
(2)The higher the silicon content in the molten iron, the lower the absorption rate of the added recarburizer.
(3)The more binders artificially added in the recarburizer, the finer the powder in the recarburizer, and the worse the absorption rate.
(4)The particle size of the recarburizer does not match the amount of melting in the electric furnace. Large particles in small electric furnaces and small particles in large electric furnaces will both affect the absorption rate.
The last thing to pay attention to is the operation of the recarburizer in casting.
Firstly,It is usually recommended to add the recarburizer to the molten iron,if put the recarburizer directly at the bottom of the electric furnace,because there is no absorption and decomposition of the molten iron, the recarburizer will not melt. The melting point of carbon is 3500°C, the recarburizer is dissolved rather than melted in the electric furnace, continued high temperature will only increase the temperature of the recarburizer. If there is no molten iron to float the recarburizer at this time, the crucible at the bottom of the electric furnace will have a high temperature,Damages, cracks, elephant feet will appear, and in severe cases, it may even cause furnace wear accidents.
Secondly,The order and time of adding recarburizer are also very important, which is a key link that affects the absorption rate and the quality of castings.When the amount of scrap steel is large and the amount of recarburizer added is large, the recarburizer should be added in batches. For example, 25 kg of recarburizer should be added, when one ton of electric furnace is produced, it should be added at least twice;Also pay attention to the time of addition, not too early. When 20% molten iron appears in the electric furnace, add the first batch of recarburizer, and the second batch of recarburizer should be added after the first batch is basically melted, but not later than 50% of the amount of molten iron. Too late, the recarburizer cannot be fully absorbed in the test time of the molten iron, which will cause the carbon test data to be inaccurate.In addition, the best dissolution temperature of the recarburizer in the molten iron is more than 1300 ℃,the carbon absorption rate of the recarburizer will be very low during the high temperature period of the electric furnace.
To sum up, in casting production, the principle of recarburization by using scrap steel to recarburize cast iron is: try to increase the amount of recarburization based on the calculation of the amount of recarburizer, which will help us control the carbon composition, because In the electric furnace smelting process, it is difficult to increase carbon, but it is easy to reduce carbon.