SiC Metallurgical Grade
Silicon carbide contains about 70% silicon, 30% carbon, and a small amount of free carbon and silicon. High-purity silicon carbide generally has a content of more than 96%. It is used for abrasive abrasives, with black, green and other colors. Ordinary silicon carbide is below 80%, with more green and other colors are distinguished. According to different color and grade silicon carbide can be classified into SiC abrasives grade and SiC metallurgical grade.
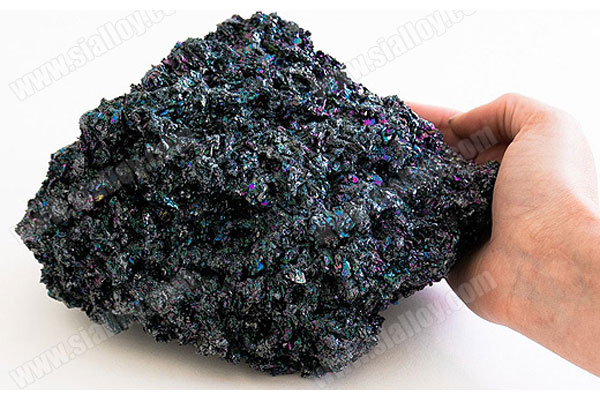
Ordinary silicon carbide is below 80%, showing more green and other colors. The melting point is also high, and the low-purity material may have too much impurities. There is also a regenerative silicon carbide, which is cheaper and is processed from old electrical components recovered from silicon carbide. In the electric furnace, it is better to use finer particles, 0.5-3 mm, so that it is easy to melt and absorb. When used in a cupola, the SiC metallurgical grade block size is larger, so as not to be washed out by strong airflow. At high temperatures, silicon carbide is decomposed into carbon and silicon ions. Their chemical properties are first reacted with oxygen, so SiC metallurgical grade reduce the oxidation of molten iron, and then enter the molten iron separately. First, they become the crystalline core of graphite. Both carbon and silicon are extremely strong. Inoculation, so they are very helpful for the melting of electric furnace and low-carbon silicon iron water. Both carbon and silicon have a strong inoculation effect, so SiC metallurgical grade are very helpful for the melting of electric furnaces and low-carbon silicon-iron water.
Silicon carbide metallurgical garde has been used more frequently in the foundry industry, and the effect is better. It can increase the graphite core, increase the number of graphite balls in ductile iron, and improve the graphite form of gray cast iron.