GPC
High-efficiency casting special recarburizer, high fixed carbon, high absorption rate, low sulfur and nitrogen, easy to absorb, effectively reduce pore inclusions, optimize graphite morphology, increase spheroidization grade, improve casting performance, and increase business benefits.
Features of our GPC recarburizer
Features of our GPC recarburizer
1. The amount of pig iron is greatly reduced, and the cost of castings is greatly reduced.
2. High temperature roasting, graphitization, high fixed carbon content.
3. The quality index is stable and the content of harmful impurities is low.
4. High absorption rate (85-95%), no residue, and more environmentally friendly.
5. No slag return, easy to control working conditions.
6. There are many graphite nuclei, good graphitization, reducing the tendency of molten iron to shrink, and improving the mechanical properties of castings.
7. The series of specifications are complete, and the product granularity can be adjusted according to customer requirements.
8. The adding method is simple and easy to operate, responsible for technical guidance and trial.
9. Widely used in the production of high-end castings abroad.
10. High cost performance, 30-35% lower than the price of the same foreign product.
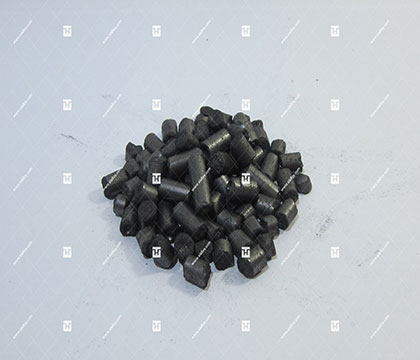
1. The influence of the particle size of the GPC recarburizer
The recarburization process using the recarburizer includes the dissolution diffusion process and the oxidation loss process. The particle size of the GPC recarburizer is different, the dissolution diffusion rate and the oxidation loss rate are also different. The absorption rate of the GPC recarburizer depends on the combined effect of the dissolution and diffusion speed of the GPC recarburizer and the oxidation loss rate: in general, the GPC recarburizer particles are small, the dissolution rate is fast, and the loss rate is large; the GPC recarburizer particles are large, The dissolution rate is slow and the loss rate is small. The choice of GPC recarburizer particle size is related to the diameter and capacity of the furnace. In general, if the diameter and capacity of the furnace are large, the particle size of the GPC recarburizer should be larger; on the contrary, the particle size of the GPC recarburizer should be smaller. For electric furnace smelting crystalline graphite below 1t, the particle size of crystalline graphite is required to be 0.5~2.5mm; for 1t~3t electric furnace to smelt the crystalline graphite particle size is 2.5~5mm; for 3t~10t electric furnace to smelt the crystalline graphite particle size requirement is 5.0~20mm; the crystalline graphite covered in the ladle is required to be 0.5 ~1mm.
2. The influence of the amount of GPC recarburizer
Under a certain temperature and the same chemical composition, the saturation concentration of carbon in the molten iron is certain. The solubility limit of carbon in cast iron is ([C%]=1.3+0.0257T-0.31[Si%]-0.33[P%]-0.45[S%]+0.028[Mn%] (T is the temperature of molten iron). Under a certain degree of saturation, the more GPC recarburizer is added, the longer the time required for dissolution and diffusion, the greater the corresponding loss, and the lower the absorption rate.
3. The influence of temperature on the absorption rate of GPC recarburizer
Analyzed from the perspective of kinetics and thermodynamics, the oxidizing property of molten iron is related to the equilibrium temperature of the C-Si-O system, that is, O in the molten iron will react with C and Si. The equilibrium temperature changes with the target C and Si content. When the iron liquid is above the equilibrium temperature, carbon oxidation occurs first, and C and O generate CO and CO2. In this way, the carbon oxidation loss in the molten iron increases. Therefore, above the equilibrium temperature, the absorption rate of the recarburizer decreases; when the recarburization temperature is below the equilibrium temperature, the saturated solubility of carbon decreases due to the lower temperature, and the dissolution and diffusion rate of carbon decreases, so the yield is also higher. Low; when the recarburization temperature is at the equilibrium temperature, the absorption rate of the recarburizer is the highest.
4. The effect of stirring of molten iron on the absorption rate of GPC recarburizer
Stirring is conducive to the dissolution and diffusion of carbon, and prevents the recarburizer from floating on the surface of the molten iron and being burned. Before the GPC recarburizer is completely dissolved, the stirring time is long and the absorption rate is high. Stirring can also reduce the holding time for carbon increase, shorten the production cycle, and avoid burning of alloy elements in the molten iron. However, if the stirring time is too long, it will not only have a great impact on the service life of the furnace, but after the recarburizer is dissolved, the stirring will aggravate the loss of carbon in the molten iron. Therefore, the proper stirring time of molten iron should be to ensure that the recarburizer is completely dissolved.
5. The influence of the chemical composition of molten iron on the absorption rate of GPC recarburizer
When the initial carbon content in the molten iron is high, the absorption rate of the GPC recarburizer is slow, the absorption amount is small, the burn loss is relatively large, and the absorption rate of the GPC recarburizer is low under a certain solubility limit. When the initial carbon content of the molten iron is low, the situation is reversed. In addition, the silicon and sulfur in the molten iron hinder the absorption of carbon and reduce the absorption rate of the GPC recarburizer; while the manganese element helps the absorption of carbon and improves the absorption rate of the recarburizer. In terms of the degree of influence, silicon is the largest, followed by manganese, and carbon and sulfur have less influence. Therefore, in the actual production process, manganese should be added first, then carbon, and then silicon.