slag inclusions of ductile cast iron
Ductile cast iron is obtained by spheroidization and inoculation treatment to obtain spheroidal graphite, which effectively improves the mechanical properties of cast iron, especially the plasticity and toughness, thereby obtaining higher strength than carbon steel. Following will introduce the slag inclusion problem in the production of ductile cast iron.
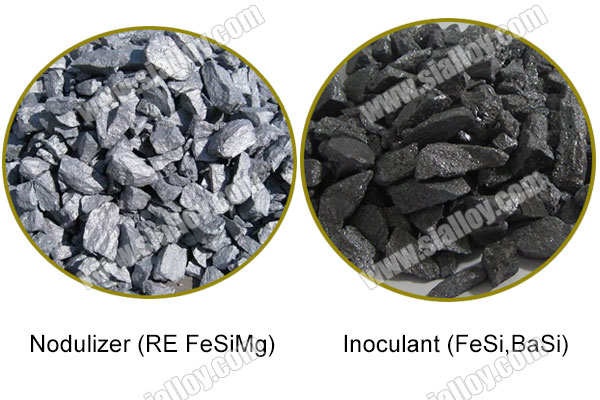
1.Influencing Factors
(1)Silicon: Silicon oxide is the main component of slag inclusion, so in order to control the slag inclusion, need to reduce the silicon content as much as possible.
(2)Sulfur: The sulfide in molten iron is one of the main reasons for the formation of slag inclusion defects in ductile cast iron. The melting point of sulfide is lower than that of molten iron. During the solidification of molten iron, sulfide will precipitate out of molten iron, increasing the viscosity of molten iron and making it difficult for molten slag or metal oxides to float up. Therefore, when the sulfur content in the molten iron is too high, the castings are prone to slag inclusion, so the sulfur content of ductile cast iron raw molten iron should be controlled below 0.06%,when it is between 0.09% and 0.135%, the slag inclusion defects of cast iron will increase sharply.
(3)RE and Magnesium: In recent years, studies have suggested that slag inclusion is mainly caused by oxidation of magnesium and RE elements, so the residual magnesium and RE should not be too high.
(4)Pouring Temperature: When the pouring temperature is too low, the metal oxides in the molten metal are not easy to float to the surface and remain in the molten metal due to the high viscosity of the molten metal; when the temperature is too high, the slag on the surface of the molten metal becomes too thin to be easily removed from the surface of the liquid, and often flows into the mold with the molten metal. In actual production, too low pouring temperature is one of the main reasons for slag inclusion. In addition, the choice of pouring temperature should also consider the relationship between carbon and silicon content.
(5)Gating System: The design of the gating system should be reasonable, with slag blocking function, so that the molten metal can fill the mold smoothly, and strive to avoid splashing and turbulence.
(6)Molding Sand: If excess sand or paint adheres to the surface of the molding sand, they can synthesize slag with the oxides in the molten metal, resulting in slag inclusion; uneven compaction of the sand mold and low compactness of the molding wall, The surface is easily corroded by molten metal and forms low melting point compounds, resulting in slag inclusion in castings.
2.Preventive Measures
(1)Control the composition of molten iron: try to reduce the sulfur content in the molten iron (<0 06%), add a proper amount of RE alloys (0 1% to 0 2%) to purify the molten iron, and minimize the silicon content and residual the amount of magnesium.
(2)Smelting process: Try to increase the temperature of molten metal from the furnace, and properly sed, to facilitate the floating and accumulation of non-metallic inclusions. Pick up the slag on the surface of the molten iron, and put a covering agent (perlite, plant ash, etc.) on the surface of the molten iron to prevent oxidation of the molten iron. Choose a suitable pouring temperature, preferably not lower than 1350℃. (3) For the pouring system to make the molten iron flow smoothly, a slag collecting bag and a slag blocking device (such as a slag screen, etc.) should be provided to avoid sand washing in the sprue.
(3)The compactness of the mold should be uniform and the strength should be sufficient; the sand in the mold should be blown off when the box is closed.
In order to manufacture high quality ductile cast iron, there are also more need to be noticed, include the elements content, inoculant and nodulizer choose and using etc, Anyang Huauto has in the raw materials for casting or foundry for more than 10 years, any requirement welcome for contact.